About Togei
Togei is one of the traditional arts of which Japan is proud and is the art of making so-called pottery. A familiar example is making a plate or a teacup.
A person who makes pottery as a profession is called a potter (陶工) or ceramicist (陶芸家).
Togei is divided into four main types: unglazed earthenware (土器) and stoneware (炻器-fired at a high temperature), glazed ceramics(陶器) and porcelain(磁器).
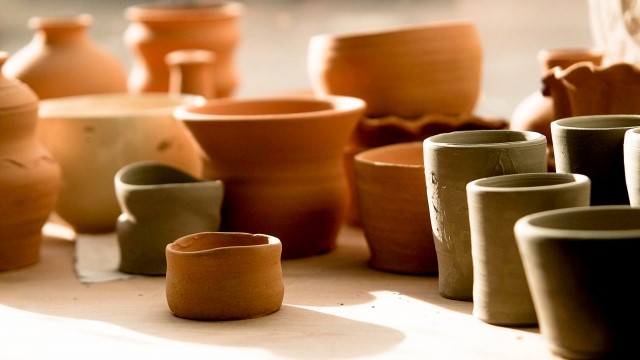
The beginning of Togei
Japan’s oldest earthenware (土器) dates back about 16,500 years before the Jomon period.
In the Jomon and Yayoi periods, only earthenware was used. Still, Japan learned the techniques from the Korean peninsula and China and made unglazed earthenware (unglazed earthenware made from the Kofun to Heian periods. blue-gray and hard) and pottery.
The technique of adding color to ceramics(陶器) with glaze was also introduced, and the Nara Sansaisai (奈良三彩), which was influenced by the Tou Sansai(唐三彩), was born in the Nara period.
During the Kamakura period, a wide variety of pottery production began in various parts of Japan. During the Azuchi-Momoyama period, when the tea ceremony flourished, teaware was born based on a unique Japanese sense of beauty.
Japan’s first porcelain(磁器) was born in the Edo period. Porcelain with brightly colored patterns on pure white fabric was exported from Imari Port and was prized by European royalty and nobility.
Nowadays, most of the products are mass-produced due to advances in forming and printing technology, but the crafts of skilled potters have a different appeal.
The main production process of Togei
The following is a rough production process.
(1) Knead the soil
The first step is to choose a good soil for the raw material. Then, let’s make them clay-like.
(2) Create a shape
Use the kneaded clay to make a shape.
(3) Drying
The shaped pieces are soft when formed. As a result, it may be deformed by a little power. So, we leave it untouched to dry and harden.
(4) Make the production unglazed
Make the production unglazed. Unglazed firing is the process of firing in a kiln in various stages without using any glaze.
(5) Apply glaze
After the baking is finished, the production is decorated with glaze. This is what makes it more beautiful.
(6) Baking (painting and baking)
There are two types of baking: oxidation firing, in which oxygen is applied to the firing (complete combustion), and reduction firing, in which the firing is done under insufficient oxygen (incomplete combustion).
(7) Completion
Completion.
How to form Togei (pottery)
There are also two main ways to shape the production. It’s “Rokuro” and “Tebineri”.
Rokuro (pottery wheel)
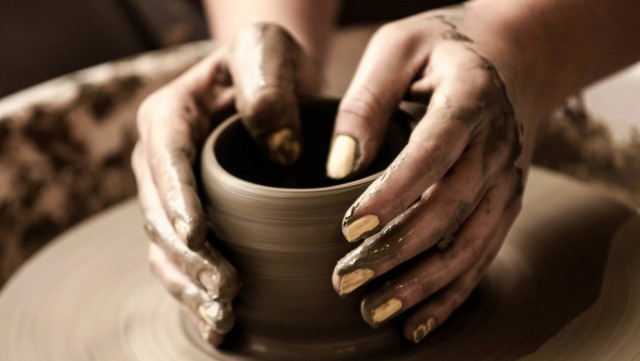
When you hear “Togei,” many people probably think of a pottery wheel. The sight of the work taking shape in front of the pottery wheel has made a strong impression on many people.
The process itself is pretty simple. First, place the clay on a stand. And then they start turning the Rokuro (pottery wheel). Using the rotation of the Rokuro, the shape of the vessel is made.
Stretch the clay, being careful not to distort the shape. Finally, the production is completed by separating it from the Rokuro.
Tebineri
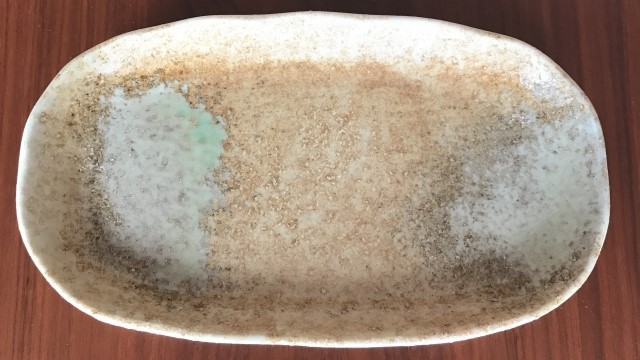
Tebineri is a method of making clay by kneading it with your hands on a table. Rokuro is suitable for making works in their natural state, rotational form.
On the other hand, the advantage of Tebineri handcrafting is that there are no restrictions on the shape of the work, and you can make it into any shape you want. A square plate is a typical example.
There is a beauty of proportionality in the works by Rokuro. On the other hand, the appeal of Tebineri handcrafting is that it allows you to create original works of art with free thinking.
Noborigama (kiln)
Noborigama is a series of chambers for firing ceramics with a fire pit at the bottom of the slope. We can bake a large amount at a time.
Photo of Noborigama
Main Places of Togei in Japan
Rokkoyou: This is the general term for the six representative ceramic kilns (Echizen, Seto, Tokoname, Shigaraki, Tanba, and Bizen) that have been in production since the Middle Ages to the present day. It was recognized as a Japanese heritage in the spring of 2017.
Seto and neighboring Mino have developed into Japan’s largest production area. In Tokoname, Bizen, Echizen, Tanba, and Shigaraki, unglazed and natural glazed pottery is still being made.
Like Arita, the birthplace of porcelain, there are kilns with various characteristics throughout Japan, such as Hagi and Karatsu, which potters opened.
We hope you’ll visit.
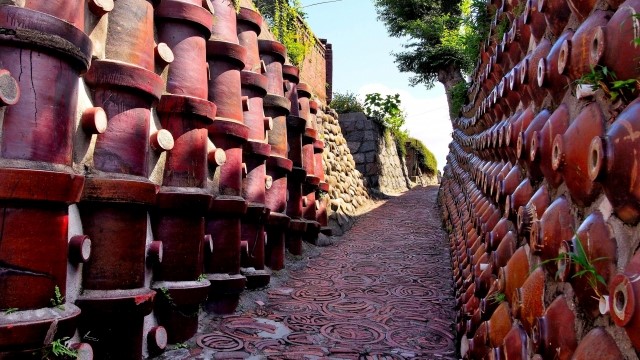